The choice between cork underlay, cork rolls and rubber cork depends on the specific needs and conditions in which the material is to be used. Below I will discuss when it is best to use each of these materials:
1. Cork underlay
Cork underlay is a thin layer of cork used primarily under various types of flooring, such as laminate panels, layered boards or carpets.
Application:
Acoustic and thermal insulation under laminate panels or floorboards: Cork underlay dampens impact and airborne sounds well, and also improves thermal comfort.
Comfort of use: Cork provides a soft and elastic surface underfoot, which increases the comfort of using the floor.
Floating floors: Ideal for floor panels and other floors installed in a floating system.
Small living spaces: Where basic acoustic and thermal insulation is needed above all, as well as reduction of noise from steps.
Main advantages:
Easy to install.
Good acoustic and thermal insulation.
Ecological.
2. Cork roll
Cork roll is an insulating material that can have different thicknesses and is available in roll form. It can be used as an underlay for floors or as a material for other applications, e.g. on walls.
Application:
Glued floors: Cork roll is often used as an underlay for glued floors, such as parquet or cork tiles. It provides good thermal and acoustic insulation, and also evens out minor unevenness of the substrate.
Decorative applications: Cork roll can be used to cover walls, create notice boards or other decorative projects.
Insulation on large surfaces: Use of cork roll on larger surfaces, such as floors of entire rooms, where better thermal and acoustic insulation is required.
Main advantages:
Versatile - can be used on floors, walls and ceilings.
Good insulating properties.
Natural appearance, which is an additional advantage in decorative applications.
3. Rubber cork
Rubber cork is a composite of cork and rubber, which is characterized by greater density, flexibility and durability than pure cork.
Application:
Highly loaded rooms: Rubber cork works great in places where the floor is exposed to heavy loads and intensive use, e.g. in offices, commercial premises, gyms or corridors.
Acoustic insulation: Rubber cork has excellent impact sound insulation properties, which makes it an ideal solution in multi-storey buildings.
Rooms with increased humidity: Thanks to the addition of rubber, rubber cork is more resistant to moisture than traditional cork, which makes it suitable for use in rooms such as kitchens or bathrooms.
Underlay for heavy floors: Rubber cork works well as an underlay for stone floors, ceramic tiles or other heavy materials.
Main advantages:
Durability and resistance to loads.
Very good acoustic insulation properties.
Resistance to moisture and temperature changes.
Summary
Cork underlay: Selected for lightweight floating floors, in apartments and where basic sound insulation and walking comfort are a priority.
Cork roll: Used under glued floors, for covering large surfaces and decorative projects where versatility and a natural look are required.
Rubber cork: Ideal for rooms with high traffic, in high humidity conditions and where exceptionally effective sound insulation and durability are needed.
The choice of the right material depends on the specific requirements for the use of the floor, the conditions in the room and the expectations regarding sound and thermal insulation.
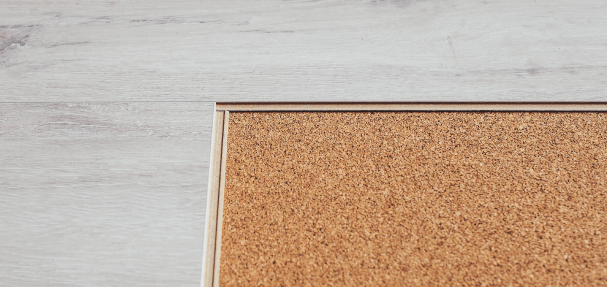
Cork underlay and cork sheets can be used on walls, but they differ in terms of thickness, function and installation method. I will discuss these differences below:
1. Cork underlay
Cork underlay is a thin layer of cork, usually 2 to 6 mm thick, available in rolls.
Wall applications:
Acoustic insulation: Cork underlay can be used on walls as a soundproofing layer, especially in rooms where we want to reduce noise transmission, such as offices, bedrooms or recording studios.
Underlay for other materials: It is often used as a backing layer for other finishing materials, such as wall panels, wallpaper or cork sheets, to increase thermal and acoustic insulation.
Ease of installation: Cork underlay is flexible and thin, which makes it easy to install on the wall. It can be glued using cork glue or assembly glue.
Limited decorative use: Due to its thinness and homogeneous structure, cork backing is rarely used as a decorative element on its own. Its main function is insulation.
Main advantages:
Easy to install.
Good sound insulation with a small thickness.
Can be used as an underlay for other finishes.
2. Cork boards
Cork boards are thicker and stiffer than cork backing, usually available in panels of 5 to 10 mm or more thickness.
Wall applications:
Decoration: Cork boards are often used as a decorative element on walls. They have a natural, warm look that adds character to interiors. They can be used on the entire surface of a wall or as accents.
Notice boards: Thanks to their thickness and stiffness, cork boards are perfect for creating notice boards or places to pin notes.
Sound and thermal insulation: Thicker cork boards offer better sound and thermal insulation than cork backing. They are particularly effective in rooms where higher insulation is required, such as music rooms or studios.
Durability: Cork boards are more durable and resistant to mechanical damage compared to cork underlays. They are also more resistant to impacts.
Main advantages:
Aesthetics and decorative.
Better thermal and acoustic insulation due to greater thickness.
Can be used as functional surfaces, such as boards.
3. Summary of differences
Thickness and function: Cork underlay is thin and flexible, mainly used as an insulating layer under other materials. Cork boards are thicker and stiffer, making them better suited as a decorative finish and in applications requiring greater insulation.
Decorative use: Cork boards are often used as a finishing element in themselves, while cork underlays mainly have a technical function.
Ease of installation: Cork underlays are easier to install due to their flexibility and thinness, while installing cork boards requires precision and is more time-consuming, but gives more aesthetic results.
Material selection
Choose a cork underlayment when the main goal is to improve acoustic or thermal insulation under another finishing material.
Choose cork boards when you want to achieve additional aesthetic benefits or need better insulation on the wall, while also being functional, e.g. as a board.
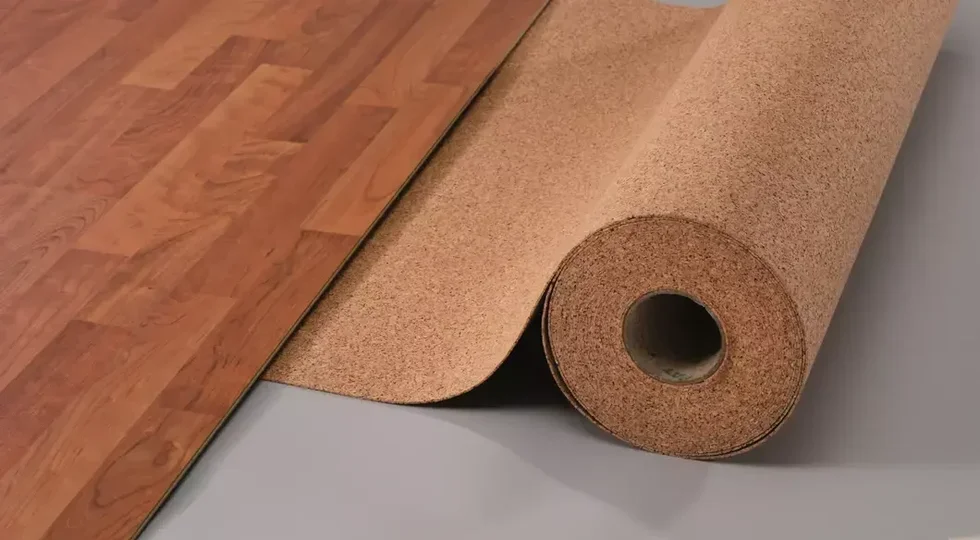
The production of cork rolls in cork factories is a complex process that begins with the collection of raw material and ends with the processing of the cork and its shaping into rolls. Here is a detailed description of this process:
1. Raw material extraction
Cork is obtained from the bark of the cork oak (Quercus suber). These trees grow mainly in Mediterranean countries such as Portugal, Spain, Italy and Morocco. The process of harvesting the bark is carried out without harming the tree, which can be harvested again every 9-12 years.
Harvesting the cork:
Harvesting the bark: The cork is harvested by hand by specialized workers who carefully separate the bark from the trunk so as not to damage the tree. The bark from the first harvest (virgin cork) is more porous and less elastic, so it is often used to produce cork granules.
Drying the bark: After harvesting, the bark is dried in the open air for a period of several weeks to several months so that it naturally gets rid of moisture and becomes more elastic.
2. Processing and preparation of cork
After initial drying, the bark is sent to the factory, where it undergoes the next stages of processing.
Cooking:
Cooking the bark: The bark is boiled in large tanks of boiling water for about an hour. This process is intended to soften the cork, increase its elasticity and remove impurities. Cooking also causes the bark to expand, which makes it easier to process further.
Cutting and milling:
Cutting: After cooking, the bark is cooled and cut into smaller pieces or granulated, depending on its intended use.
Milling: Corks that are not suitable for direct use are ground into cork granulate, which will later be re-formed. The granulate can be the final product or can be used to produce other cork products.
3. Production of cork rolls
The production of cork rolls requires several key stages that are essential to obtaining a final product with the right properties.
Granule Forming:
Mixing: The cork granules are mixed with natural or synthetic binders that help bind the material into a uniform mass.
Block Forming: The granulate and binder mixture is formed into large blocks or sheets, which are then compressed under high pressure and at high temperature. This process is called cork agglomeration. The blocks produced have a very dense and compact structure.
Roll Manufacturing:
Sheeting: After cooling, the cork blocks are cut into thin sheets of the thickness that corresponds to the planned cork rolls.
Winding: The cork sheets are wound onto rolls. This process requires precise control of the material tension to avoid cracks and deformations.
Cutting: Finally, the rolls are cut to the correct width and length as per the customers’ requirements.
4. Quality Control
Quality control is carried out after the cork rolls are manufactured. The following are checked:
Material thickness and uniformity: Each roll must have an even thickness along its entire length.
Density: The even density of cork is crucial for its insulating properties.
No defects: The rolls are checked for cracks, holes or other defects on their surface.
5. Packaging and distribution
After quality control, the rolls are packed in a way that protects them from damage during transport and storage. They are then sent to distributors, stores or directly to customers.
6. End use
The cork roll is ready for use and can be used in a variety of applications, such as:
Thermal and acoustic insulation: Used under floors, on walls or ceilings.
Decorative surfaces: Cork rolls can be used to cover walls for aesthetic purposes.
Notice boards: Cork rolls are used as a material for creating information boards.
The production of cork rolls is a process that combines traditional methods of cork harvesting and processing with modern processing technologies, which allows for obtaining durable and versatile products that are used in many areas.